Unlock the secrets of embroidery digitizing with this detailed guide, designed for both beginners and advanced users. From basic techniques like flat and monogram digitizing to advanced methods like 3D puff and metallic thread, this guide covers everything you need to know. Learn about software tools, solve common challenges, and explore emerging trends in the embroidery world. Perfect for hobbyists and professionals seeking to refine their digitizing skills.
1. Introduction to Embroidery Digitizing
2. Basic Types of Embroidery Digitizing
– Flat Embroidery Digitizing
– 3D Puff Embroidery Digitizing
– Appliqué Digitizing
– Monogram Digitizing
– Patch Digitizing
3. Advanced Embroidery Digitizing Techniques
– Shading and Gradients in Embroidery
– Color Blending and Layering
– Embossed Embroidery Digitizing
– Metallic Thread Embroidery
– Sequins and Beads in Embroidery
4. Specialty Embroidery Digitizing
– Chenille Embroidery Digitizing
– Chain Stitch Embroidery
– Tackle Twill Embroidery
– Cross-Stitch Embroidery Digitizing
5. Software and Tools for Embroidery Digitizing
– Popular Embroidery Digitizing Software
– Essential Tools for Digitizing
– File Formats and Compatibility
– Understanding Stitch Types: Fill, Satin, and Running Stitches
6. Step-by-Step Guide to Digitizing Different Types of Embroidery
– Preparing the Artwork
– Choosing the Right Stitch Type
– Adjusting for Fabric Type
– Practical Examples and Case Studies
7. Common Challenges in Embroidery Digitizing
– Avoiding Thread Breakage
– Managing Complex Designs
– Optimizing for Speed and Quality
– Troubleshooting Common Issues
8. Tips and Best Practices for Successful Embroidery Digitizing
– Understanding Thread Tensions
– Handling Small Lettering and Details
– Maximizing Durability and Longevity of Embroidered Designs
– Testing and Final Adjustments
9. Industry Applications of Different Embroidery Digitizing Types
– Apparel Industry
– Home Décor
– Promotional Products and Corporate Branding
– Personalized Gifts and Crafts
10. Future Trends in Embroidery Digitizing
– Eco-Friendly Embroidery Techniques
– Automation and AI in Embroidery Digitizing
– Emerging Design Trends
11. Conclusion
– Summary of Key Takeaways
– Final Tips for Embroidery Digitizers
1. Introduction to Embroidery Digitizing
What is Embroidery Digitizing?
Embroidery digitizing converts artwork or images into a digital format that embroidery machines can read and stitch onto fabric. This process involves translating design details into specific types of stitches and commands for the machine to follow. It’s a crucial step in creating high-quality embroidery designs that maintain the original visual aesthetics while being stitchable on fabric.
The Importance of Digitizing in Modern Embroidery
Digitizing has transformed the embroidery industry, allowing intricate designs to be produced with precision and speed. It enables businesses to offer customized apparel, corporate branding, and personalized gifts, ensuring consistency across mass production. By mastering digitizing and vector artwork, embroiderers can improve their craft, reduce errors, and produce designs that enhance the quality and appearance of the final product.
Who Uses Embroidery Digitizing?
Many professionals utilize Embroidery digitizing, including fashion designers, embroiderers, businesses offering custom apparel, and even hobbyists. From large-scale commercial operations to small crafting enterprises, the ability to create digitized embroidery designs enables a versatile approach to producing high-quality, customized pieces efficiently.
2. Basic Types of Embroidery Digitizing
Flat Embroidery Digitizing
Flat embroidery is one of the most common types. Designs are stitched directly onto the fabric surface, creating a smooth and flat finish. It’s widely used in logos, patches, and personalized apparel. The key to successful flat embroidery digitizing is choosing the right stitch type (e.g., satin or fill stitches) and ensuring the design maintains clarity at various sizes.
3D Puff Embroidery Digitizing
3D puff embroidery involves adding foam under the stitches to create a raised, three-dimensional effect. This type of embroidery is popular for caps, jackets, and other items where a bold, eye-catching design is desired. Digitizing for 3D puff requires specific settings, such as increased stitch density and careful spacing, to prevent foam from showing through.
Appliqué Digitizing
Appliqué embroidery digitizing involves layering fabric pieces onto a base material and securing them with stitching. This technique allows for using different textures and colors in a single design. When digitizing for appliqué, it’s important to create outlines that guide the cutting and placement of fabric, ensuring precise alignment during stitching.
Monogram Digitizing
Monogramming is the art of embroidering initials or a combination of letters onto fabrics, often for personalization. Monogram digitizing requires attention to letter spacing, font style, and stitch type, ensuring each letter stands out clearly. It’s commonly used in towels, linens, and uniforms for a professional or personalized touch.
Patch Digitizing
Patches are standalone embroidered designs that can be attached to garments or accessories. Patch digitizing typically involves creating a border around the design and utilizing a dense stitch for the main elements. Because patches may feature intricate details, the digitizing process should optimize clarity and durability when the patch is stitched onto various fabrics.
3. Advanced Embroidery Digitizing Techniques
Shading and Gradients in Embroidery
Shading and gradients add depth and realism to embroidery designs. Digitizing shading involves varying stitch lengths and densities to mimic gradual color changes. This technique is ideal for complex designs like portraits or landscapes, where natural variations in color are essential to achieving a high level of detail.
Color Blending and Layering
Color blending in embroidery digitizing allows for smooth transitions between colors, creating a layered effect. By strategically overlapping stitches in different thread colors, digitizers can simulate a blended look, ideal for designs requiring subtle in color, such as floral or abstract art.
Embossed Embroidery Digitizing
Embossed embroidery creates a raised effect by stitching around a design, allowing the fabric beneath to form the pattern. This technique is commonly used on towels, robes, and other textured fabrics. Digitizing for embossed embroidery requires careful control of stitch depth and density to achieve the desired raised effect without damaging the fabric.
Metallic Thread Embroidery
Metallic thread adds a shiny, reflective quality to embroidery. However, metallic threads can be challenging due to their tendency to break. When digitizing for metallic threads, reducing stitch density and avoiding complex shapes is crucial to prevent thread breakage and ensure a smooth, polished finish.
Sequins and Beads in Embroidery
Sequins and beads add texture and sparkle to embroidery designs. Digitizing for sequins requires specialized software that can control the placement of sequins at precise intervals. Similarly, beads are often added by hand, but digitizing can dictate the stitch patterns needed to secure them, enhancing the final design with tactile elements.
4. Specialty Embroidery Digitizing
Chenille Embroidery Digitizing
Chenille embroidery produces a soft, fuzzy effect, commonly seen in varsity jackets and patches. This type of embroidery uses yarn rather than thread, and digitizing for chenille requires adjusting stitch settings to accommodate the thickness and texture of the yarn, ensuring even coverage and durability.
Chain Stitch Embroidery
Chain stitch embroidery is a decorative technique where stitches form a chain-like pattern. It’s used in artistic embroidery and high-end fashion. Digitizing chain stitch designs requires understanding how the stitches loosen together, allowing for smooth curves and intricate details that enhance the visual appeal of the final product.
Tackle Twill Embroidery
Tackle twill combines embroidery with twill fabric pieces, often used in sports jerseys and uniforms. Digitizing for tackle twill involves creating a pattern that can be laser-cut and sewn onto the garment, along with embroidery stitches to secure the twill in place. The result is a durable, high-contrast design for team names and numbers.
Cross-Stitch Embroidery Digitizing
Cross-stitch embroidery uses X-shaped stitches to create intricate patterns. While traditionally done by hand, digitizing cross-stitch allows for more complex and precise designs. The digitizing process involves setting the machine to follow a specific grid pattern, ensuring each stitch is placed correctly to form the design.
5. Software and Tools for Embroidery Digitizing
Popular Embroidery Digitizing Software
Various software tools, such as Wilcom, Brother PE-Design, and Hatch Embroidery, are available to digitize embroidery designs. Each software offers unique features, including stitch simulation, design editing, and automatic stitch generation, making it easier to turn artwork into digitized embroidery files.
Essential Tools for Digitizing
In addition to software, digitizers require graphic design software (e.g., Adobe Illustrator) to prepare vector files, a reliable computer, and embroidery machines compatible with different file formats. These tools help ensure that designs are created efficiently and can be easily transferred to the embroidery machine.
File Formats and Compatibility
Embroidery digitizing files come in various formats, such as DST, PES, and EXP. It’s important to understand the compatibility of different formats with embroidery machines. For example, some machines may only accept certain formats, so digitizers must ensure the design is saved correctly to avoid issues during production.
Understanding Stitch Types: Fill, Satin, and Running Stitches
Embroidery digitizing involves several stitch types: fill stitches cover large areas, satin stitches create smooth, raised edges, and running stitches are used for outlines and details. Each stitch type serves a specific purpose in the design, and the digitizer must choose the right stitch type based on the fabric and the design requirements.
6. Step-by-Step Guide to Digitizing Different Types of Embroidery
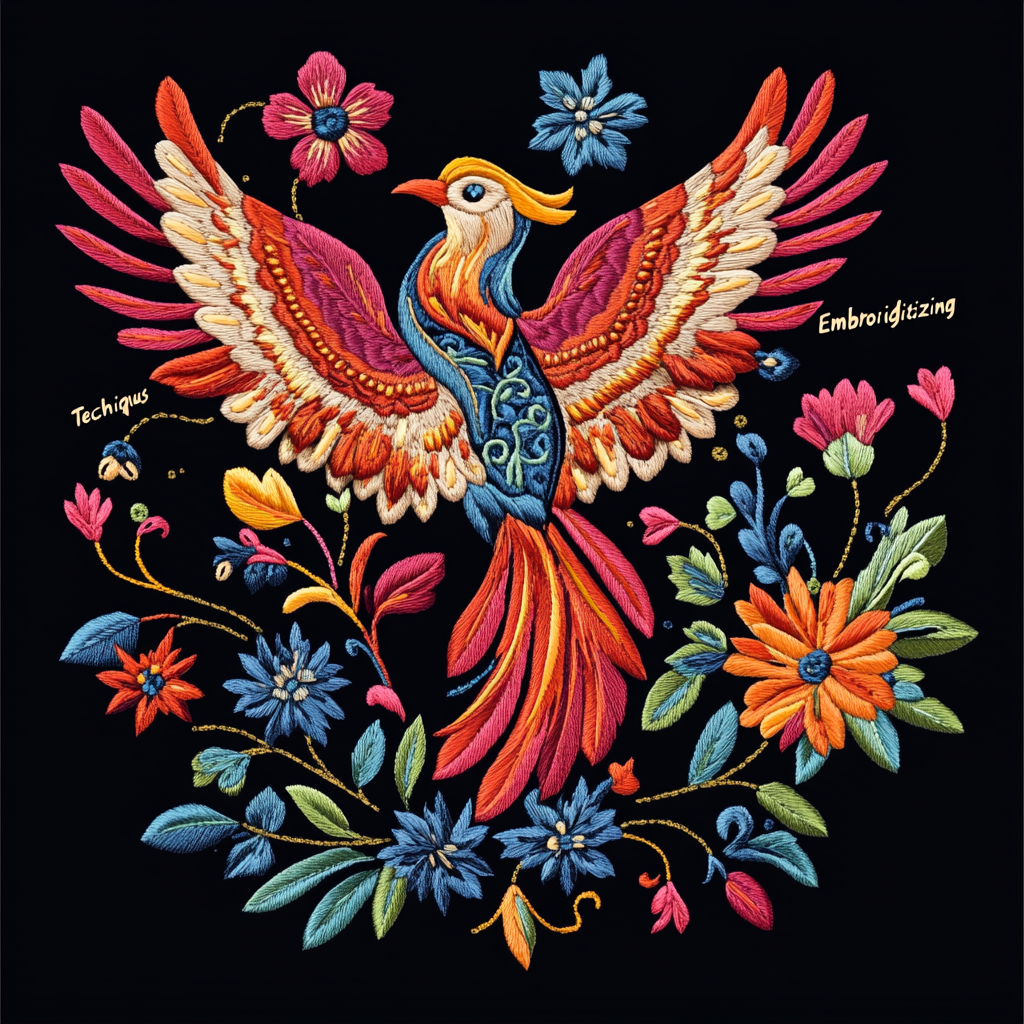
Preparing the Artwork
Before digitizing, it’s essential to prepare the artwork, ensuring it is in a format suitable for digitizing, such as vector files. High-resolution images or clean, well-defined designs yield the best results. Scaling the artwork to the final size and considering color separations are also important steps.
Choosing the Right Stitch Type
The choice of stitch type depends on the design elements, fabric type, and the desired effect. For example, satin stitches are ideal for borders and text, while fill stitches are suitable for covering large areas. A well-digitized design will balance stitch types to achieve both durability and aesthetics.
Adjusting for Fabric Type
Different fabrics require different digitizing settings. Stretchy fabrics like T-shirts may need underlay stitches to stabilize the design, while heavier fabrics like denim can handle denser stitch patterns. Digitizing must account for fabric properties to prevent puckering or distortion.
Practical Examples and Case Studies
Practical examples help illustrate how different digitizing techniques are applied in real-world projects. For instance, a case study on digitizing a corporate logo for a uniform could highlight the choice of stitch types, color considerations, and fabric adjustments.
7. Common Challenges in Embroidery Digitizing
Avoiding Thread Breakage
Thread breakage is common in embroidery, often caused by improper tension, overly dense stitches, or poor-quality thread. Experts Digitizers can prevent breakage by ensuring proper stitch density, using high-quality thread, and adjusting machine settings for optimal performance.
Managing Complex Designs
Complex designs with intricate details can pose a challenge during digitizing. Simplifying the artwork, adjusting stitch types, and minimizing thread changes can help manage complexity. Additionally, testing the design on fabric before full production is critical to identifying any potential issues.
Optimizing for Speed and Quality
Balancing speed and quality is essential in embroidery production. Digitizers must optimize designs for the fastest possible stitch time without compromising quality. This involves reducing unnecessary stitches, minimizing thread changes, and adjusting stitch density based on fabric and design complexity.
Troubleshooting Common Issues
Common digitizing issues include misalignment, puckering, and thread tension problems. Troubleshooting these issues involves checking the design’s stitch settings, fabric compatibility, and machine calibration. For example, misalignment can often be corrected by adjusting the stitch direction or adding underlay stitches for stability, while puckering may be reduced by modifying stitch density or tension settings.
8. Tips and Best Practices for Successful Embroidery Digitizing
Tips and Tutorials for Embroidery Digitizing: Embroidery digitizing involves transforming artwork into stitch patterns for embroidery machines. To achieve high-quality results, starting with clear, vector-based images is essential. Understanding different stitch types and their suitability for various designs is crucial. Optimizing your digitization for the specific fabric you’ll be using is important to ensure proper thread placement and stitch density. Always test stitch a sample of your digitized design to identify and address any issues before finalizing it. Lastly, investing in reliable embroidery digitizing software can significantly streamline the process and provide advanced features for creating intricate designs.
Understanding Thread Tensions
Correct thread tension is crucial for achieving clean, professional-looking embroidery. Too much tension can cause the fabric to pucker, while too little can result in loose, uneven stitches. Understanding how the design interacts with the fabric and machine tension settings during the digitizing process helps create optimal stitch quality.
Handling Small Lettering and Details
Small lettering and intricate details are challenging to digitize, especially for designs meant for fabrics like caps or t-shirts. Digitizers should use thicker fonts to ensure clarity, increase stitch density, and avoid overly complex designs. Testing small text on the chosen fabric also helps determine whether adjustments are needed before full-scale production.
Maximizing Durability and Longevity of Embroidered Designs
Ensuring that embroidered designs are durable involves careful digitizing and material selection. By choosing the right stitch density, using underlay stitches to prevent fabric stretching, and selecting strong, high-quality threads, digitizers can improve the longevity of the embroidery, even after repeated washing or wear.
Testing and Final Adjustments
Testing designs before final production is a critical step in the digitizing process. A test run on the intended fabric helps identify any issues with stitch density, alignment, or compatibility. Based on the test results, the digitizer can make adjustments to ensure the final product meets quality standards and customer expectations.
9. Industry Applications of Different Embroidery Digitizing Types
Apparel Industry
Embroidery digitizing plays a significant role in the apparel industry, particularly for custom clothing and uniforms. Companies use embroidery to brand their apparel with logos, monograms, and names, making digitized designs essential for high-quality, durable branding solutions.
Home Décor
Embroidery digitizing is also popular in home décor, including cushions, curtains, and towels. Designs used in home décor often incorporate intricate details and larger formats, which require specialized digitizing techniques to ensure the best stitch quality on various fabrics.
Promotional Products and Corporate Branding
Businesses frequently market their brands using embroidered promotional products like hats, bags, and jackets. Digitizing ensures company logos and designs are consistently reproduced across products, providing a professional appearance. Digitizers often focus on maintaining design clarity and durability when producing promotional materials.
Personalized Gifts and Crafts
Personalized embroidery is popular for gifts and crafts, such as monogrammed towels, custom patches, and embroidered artwork. Digitizing’s versatility enables hobbyists and professionals to create custom designs that can be applied to almost any fabric, allowing endless creative possibilities.
10. Future Trends in Embroidery Digitizing
Eco-Friendly Embroidery Techniques
As sustainability becomes a priority, eco-friendly embroidery techniques are emerging. Embroidery Digitizers can reduce waste by optimizing thread usage and minimizing errors during production. New types of sustainable threads and biodegradable fabrics are also being developed, allowing for more environmentally conscious embroidery options for embroidery digitizing services companies.
Automation and AI in Embroidery Digitizing
Automation is rapidly changing the landscape of embroidery digitizing. With the help of AI, software is becoming more intuitive, offering automatic design optimization and even self-correcting features. This reduces the manual effort required and improves accuracy, allowing even beginners to achieve professional results.
Emerging Design Trends
Design trends in embroidery continue to evolve, emphasizing personalized, intricate, and artistic creations. From minimalist designs to more complex, three-dimensional patterns, digitizers must stay current with emerging trends to remain competitive. This requires creativity and an understanding of how to leverage digitizing software effectively.
11. Conclusion
Summary of Key Takeaways
Embroidery digitizing is a multifaceted craft that combines artistic design with technical precision. From basic types like flat and monogram digitizing to advanced techniques like shading, color blending, and 3D puff, understanding the principles behind each type of digitizing ensures successful embroidery projects. With the right tools, knowledge, and practice, digitizers can create beautiful, high-quality designs that stand the test of time.
Final Tips for Embroidery Digitizers
To excel in embroidery digitizing, focus on continuous learning and practice. Stay updated on the latest software developments and industry trends. Always test your designs before full production to avoid costly errors. Whether digitizing for commercial purposes or personal projects, patience and attention to detail will help you achieve professional, lasting results. Learn about the terminology of embroidery digitizing.